I admire people who love what they do. There’s a lot of truth to the oft-quoted Mark Twain observation: “Find a job you enjoy doing, and you will never have to work a day in your life.”
“Find a job you enjoy doing, and you will never have to work a day in your life.”
For the most part, that applies to me. But my friend Mike Gentry, VP and principal consultant of Quality Consulting, is truly living the dream. He doesn’t just assess quality for his day job, he looks forward to weekend opportunities to ply his craft.
“When I go into companies and I talk to them, I’m kinda weird because I get excited about quality,” he said. “When I walk in and I’m like, ‘Are you ready to have some fun?’ They’re like, ‘Uh, no, you’re auditing me.’”
But Gentry is undaunted and his enthusiasm is unflagging—maybe even contagious.
“I understand quality is a dry subject. A lot of people really don’t find it fascinating. I do,” he said. “One of my jobs, when I consult with somebody about their quality management systems, is to try to get them to understand it and the importance of it enough to also get excited about it, at least to the point they also want to get something out of their quality management system.”
Gentry was more than happy—excited, even—to teach a quick history lesson on quality systems and ISO certifications. The concept of quality control really took root in 1926 with the International Federation of National Standardizing Associations, the forerunner of modern ISO. In 1946, that organization met with delegates from the United Nations Standards Coordinating Committee to form a new global standards body, the International Organization for Standardization, and the new organization began official operations in 1947.
“Initially, ISO standards were much more prescriptive,” Gentry said. “A lot of companies felt that ISO was basically telling them how to run their companies, or how to conduct their business, through telling them the specifics of how to perform the associated processes. As time has progressed, however, the ISOs have transitioned into becoming less prescriptive and less invasive on the specifics of how a company functions via its quality management system.”
Gentry also told me ISO is not short for International Standards Organization or any other group. It’s from the Greek word “isos,” which means “equal.” The ISO standards on everything from orthopedic implants to office furniture are there to reassure that item is crafted to meet specific standards of quality associated with that product, no matter where it comes from.
“It doesn’t mean their systems are all set up the same, it means they’re following a standard when they’re doing the manufacturing or testing and that quality checks are in place,” Gentry said.
“Hopefully, I get the same quality of product in Denmark as in the U.S. or China. It’s [the idea that] it’s equal product, equal quality.”
Quality systems are fundamentally about mindset, Gentry said. Processes are important, but the goal is to provide the best possible product. Linda Braddon, CEO of Secure BioMed Evaluations, believes the best quality systems are simple.
“We have a very minimalist approach,” she said. “What we have found over the years is when we go in and [a client is] messy or has 483s, warning letters, or are under consent decree for FDA or have a warning letter, it is almost always because their quality system is so complicated their staff shuts down. When you make the rules so hard to obey, people don’t try harder to obey, they stop paying attention.”
It’s easy to add complexity, she said. But if you keep a quality system simple, people are more likely to understand and follow it. She also encourages her customers to see audits and even warning letters as opportunities. It’s all a work in progress, she said.
“The point [of a quality system] is that it’s about continuous improvement,” she said. “We’re going to try very hard [to pass audits], but sometimes they bring up a great point. Sometimes you get a nonconformance and you fix it and you learn something.”
Braddon’s company is unique. It’s the only outsourcing option for quality systems that she or I know of. Thanks to an increasingly paperless world, she’s able to get documents signed electronically and stay in close contact with clients. She said it’s a practical option for smaller companies without the budget or depth of expertise to develop and maintain quality systems in-house.
“Good quality and regulatory people are a nightmare to find and keep,” she said. “We become our client’s outsourced quality staff because they couldn’t do it more cost effectively. At some point, they’ll integrate. Usually at that point, it’s because they’re either selling or hiring staff for maintenance. But there’s probably a good two to five years where we’re a really highly seasoned, cost-effective solution.”
Regardless of how or where you maintain your quality system, the best ones engage employees across ranks and job functions, Gentry said.
“You do want everybody to understand why they have the quality system,” he said. “The quality manager absolutely knows the quality system. But that’s not the intention. The intention is that those policies flow from the top down.”
Gentry said he often finds smaller companies are much more engaged in regulatory processes and much more likely to eventually join him in his excitement about audits.
“A percentage of the larger companies—not all of them, of course—seem to engage their quality system more in order to sell product, which, of course, is the goal of any company,” he said. “I get more questions about how to meet the minimum requirements from larger companies.”
And those smaller companies also tend to have simpler systems, he said.
“It’s been my experience that the smaller companies really engage their quality system to be as simple as possible, but they also expect that system to provide maximum value to both their company and to their customer,” Gentry said. “I normally see good excitement and lots of ‘a-ha moments’ from smaller companies that realize what putting that quality system in place means for their customers, and for their company as well, as we create that quality system and as we ‘tweak’ and customize it.”
Braddon agreed. Larger companies are more likely to build in more complex quality systems that can in some cases create compliance hurdles, she said.
“I think the large companies with very burdensome quality systems are what people find very hard to execute,” she said. “I think the level of engagement is different from the small startup with very passionate people, the ones where your CEO has every cent of his savings sunk into it is going to care more about the end product more than the person drawing a salary from a job.”
For Braddon, building a strong partnership is key to creating that top-down flow. Frequent, open communication is key to managing multiple systems for a range of clients, she said.
“We don’t act like consultants, we act like staff, like trusted partners,” she said. “It’s important to hire people that you like and have confidence in. Sometimes the decisions are hard. There are times I say, ‘You just have to trust me. I can’t defend this in an audit.’ If you’re going to work with us and partner with us, you need to be doing so because you believe we have your best interest at heart, we understand the rules, and we’re always considering the patient.”
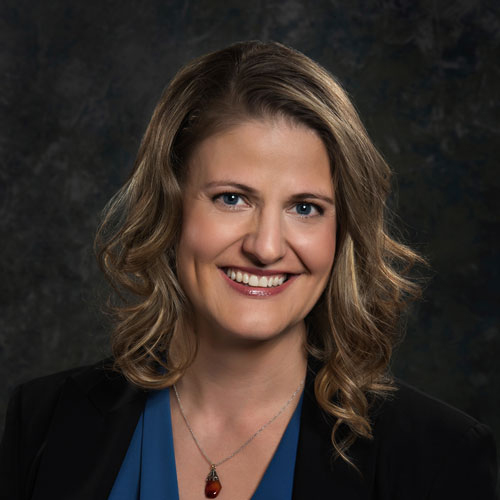
Dawn Lissy is a biomedical engineer, entrepreneur, and innovator. Since 1998, Empirical Technologies Corp. has operated under Lissy’s direction. Empirical offers the full range of regulatory and quality systems consulting, testing, small batch and prototype manufacturing, and validations services to bring a medical device to market. Empirical is very active within standards development organization ASTM International and has one of the widest scopes of test methods of any accredited independent lab in the United States. Because Lissy was a member of the U.S. Food and Drug Administration’s Entrepreneur-in-Residence program, she has first-hand, in-depth knowledge of the regulatory landscape. Lissy holds an inventor patent for the Stackable Cage System for corpectomy and vertebrectomy. Her M.S. in biomedical engineering is from The University of Akron, Ohio.